By Douglas Hart, CMRP, Senior Consultant, Reliability Insights
June 2021
The Problem- It is the perfect storm; an aging workforce is preparing to retire in the midst of a soft economy where many companies have paused, if not altogether halted, their Maintenance training efforts. Meanwhile, a newer and younger workforce is entering the marketplace largely untrained and yet responsible for maintaining the most complex and expensive equipment with less scheduled access to these assets than any time in history.
With the impending baby boomer exodus during a highly competitive global market, it is imperative that industrial and manufacturing organizations utilize highly skilled Maintenance resources to reliably maintain their critical equipment and processes.
If the younger and largely inexperienced and undertrained maintainers do not obtain the skills necessary to quickly and accurately diagnosis, repair, and maintain critical equipment and processes, companies will pay an incredibly high price in terms of lost production, waste, materials expenses, customer satisfaction, reputation within the market, and overall profitability.
For more than a decade, there has been a void in the American maintenance training landscape. Many organizations eliminated the dedicated Maintenance Training roles, delegating those under-valued and often over-looked responsibilities to either the Maintenance leadership personnel or in some cases to the human resources staff. In either case, it has resulted in a neglected effort in performing any consistent and effective training for the majority of maintenance personnel.
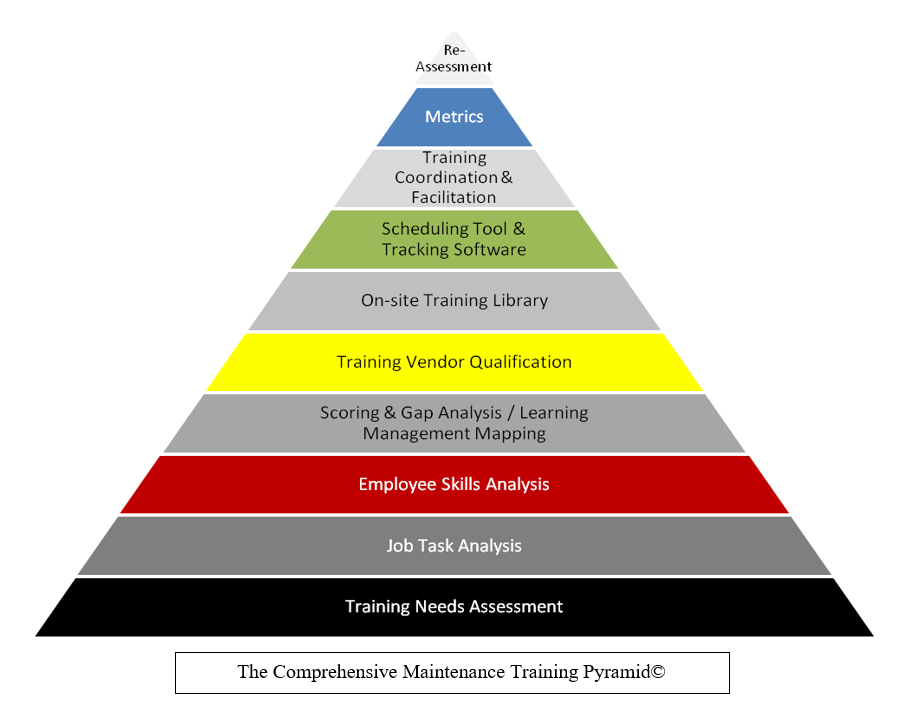
Little effort has been expended in identifying the unique skill sets required to properly maintain a specific site’s critical assets and systems and seemingly less effort has been spent ensuring the Maintainers have been trained to properly diagnose and remedy recurring asset care issues.
It is imperative that the industrial and manufacturing community change their perspective of the importance of craft training and realize they can NEVER operate as cost-effectively and reliably without investing in their Maintenance and Reliability personnel. And that does not mean just throwing dollars at a Training program. On the contrary; it means that a thoughtful, innovative and strategic Maintenance Training process should be developed. Some of those key elements include the following items.
The Details-
1. Training Needs Assessment:
It is important to start with an objective Maintenance Training Needs Assessment (TNA) that focuses on key areas to address in developing your comprehensive Maintenance training effort. At a high level, the TNA encompasses three key areas:
- The first involves the process of selecting the critical systems and assets at your facility in which the site personnel are responsible for Maintaining. If an asset criticality ranking has been performed previously, that is an excellent place to start your review.
-
Secondly, gaining an understanding of recurring asset failures will aid in narrowing your focus of which skill sets to concentrate on developing. In addition to asking both Operators and Maintainers which recurring equipment failures they are aware of, do not forget to use your site’s Computerized Maintenance Management System (CMMS). By mining the CMMS database for recurring Corrective Work Orders, you may uncover some surprisingly time-consuming equipment that has taxed your site personnel over the years, and they should be included in your list. Be sure to search for the most common Failure Codes, Bad Actors and Reason For Outage (RFO) attributes. This can be a very insightful process so be sure to communicate any value-added findings with your Maintenance Management and Reliability Engineering personnel.
-
Finally, an identification of which skill sets are required to maintain those identified critical and frequently failing systems and assets should be captured. Although there are over 60 industrial and manufacturing skill sets required, it is beneficial to identify the top 10-20 at your site to begin focusing on.
2. Job Task Analysis:
Once a TNA has been performed, it is time to conduct a Job Task Analysis (JTA). A JTA will assist in further defining the critical skills you need to develop at your site. By conducting a review of the Maintenance activities, Job Plans and Work Instructions associated with the critical and periodically failing equipment you identified in the TNA, you will identify very specific skills required to perform maintenance or repairs at your site. This information should be used to round out the top skill sets to be developed at your facility.
3. Employee Skills Analysis:
Once you have identified the prioritized skills required to properly maintain your critical processes and assets, it is time to find out how the current team responsible for possessing these skills are equipped. Although the mention of conducting skills assessments can be met with varying degrees of interest and support, it needs to be clear that the intent is not to perform a witch hunt in an effort to “slap someone’s hands” if they do not test in the range required to perform accurate, safe, sustainable and work done right the first time. But rather, it is to ensure that the investment of future training time and training funds are properly spent. Remember, if you or I were paying for the team’s training, we would want to ensure we are spending that investment in the right areas of developing competency.
You may also get some pushback in the area of job descriptions. If your current position descriptions are too vague or outdated, they may need to be addressed first prior to pursuing the skills assessment. It only makes sense to correct these before moving forward.
There is always the consideration of the value of paper or on-line testing vs. the expense of actually demonstrating proficiency on field simulators. That is a consideration you will want to give some thought to. The prevailing mindset is to use on-line skills testing for basic competencies and save the select few (and more expensive) testing on simulation equipment for more highly developed disciplines.
4. Scoring & Gap Analysis / Learning Management Mapping:
Once the agreed upon skills assessments are performed, it is time to review where the training opportunities reside and map out a training mitigation plan. Ideally this is done by person. If, however, your organization is so large or does not allow the individuals to be specified, the next best option is to develop the learning plan schedules by craft (Mechanical, Electrical, etc.). Effort should be given to confirm the alignment between the recent low scoring test areas and the specific future training that will be provided.
Developing a realistic and customized training plan is important. Be sure to not be too aggressive in scheduling time for training and do not forget to notify the Maintenance Schedulers about getting this training into their calendars.
5. Training Vendor Qualification:
Based upon the outcome from the identified required future training for your site, the next step is to locate qualified Maintenance training organizations and programs which leverage the best-of-the-best in each required training area. Although it is tempting to just source one or two training resources to complete this step, it will likely require utilizing multiple organizations to get targeted and effective training, based on the various needed competencies to develop. Just be prepared that there is seldom a “one stop shop”.
6. On-site Training Area:
Where applicable, it may make sense for your organization to develop an on-site training area to store training materials and provide a dedicated place for certain training sessions to occur. This effort will range from identifying the optimum space and location of the area to encompassing the simulation labs, shelving, tables, chairs, computers, training materials and check-out procedures.
7. Scheduling Tool & Tracking Software:
Based on the size of your Maintenance staff, you will want to consider adopting the use of a scalable Learning Management System (LMS) to schedule and document actual training events per employee or craft. This electronic repository is ideally suited to capture the details of the site’s Maintenance training program and serves as an excellent source of documentation for site leadership or for organization’s affiliated with regulatory considerations.
8. Training Coordination & Facilitation:
Based on the size of your staff to be trained, the organizational roles and responsibilities at your disposal and the level of LMS you may have in place, the level of effort to manage your training program to ensure it is effective and sustainable will vary. It has certainly been a noticeable trend over the past decade for the traditional Maintenance Training Coordinator to be almost non-existent. Keep in mind that if your organization is extremely lean then contracting out this part-time effort may be a viable option. It is certainly better than allowing the training initiative to simply die out.
9. Training Metrics:
In terms of adopting training metrics, you may want to consider the following elements:
-
Agree on a handful of site Training-related metrics to start tracking. Although there are approximately 20 that could be utilized, sometimes the “less is more” approach makes sense. They should be based on what is important to your facility. Remember the old saying- “To INSPECT what you EXPECT”.
-
Identify an owner to measure and report performance on a regular basis. Someone needs to champion this effort, or it can quickly fall by the wayside.
-
Ensure the KPI’s are being communicated up the organization to demonstrate value and justify future training program funding. It will be advantageous to periodically “check in” with those on the distribution to ensure reviews are occurring and to answer any questions the leadership team may have.
-
Locate the optimal places to post the tracked performance measurements. Selecting high-visibility areas generally makes the most sense.
-
The most important element is to ensure you are able to objectively and accurately measure and communicate the impact the Maintenance Training initiative is having on your operation.
10. Reassessment & Training Value Identification:
Although you have likely accomplished a great deal of improvement in your site’s Maintenance Training program by this point, like any initiative that has been in place for a period of time, it is always a good idea to perform an objective Assessment to ensure there are not gaps which need to be addressed. Remember, a large expenditure of time, effort and dollars do not guarantee success in every area. It is always a good idea to check and see which areas are requiring a little more attention.
Conducting another employee Skills assessment 18-24 months after the first one is also advisable. This will allow you to refocus in areas that still need attention and to celebrate achievements accomplished in the other areas. It is not realistic to assume that one pass at providing training after identifying skills deficiencies will get the job done. Realistically, it will require a few re-assessments over the years before you can know with surety the workforce is adequately trained.
A re-assessment will also validate the effectiveness of your new Training process and provide insight into areas to consider focusing on in the future. Best practices initiatives are typically dynamic.
Closing- Like most effective and sustainable initiatives, they do not happen quickly. Manage expectations by recognizing you did not get in the position you are in and so you will not “turn the ship around” overnight. Be patient, be consistent and realize that developing life-long skills in your team members is one of the most respected and value-added achievements you can undertake. Stay the course and may you reap the rewards of pursuing continuous improvements by implementing an innovative and effective Maintenance Training model.