By Shane Turcott, P.Eng., M.A.Sc., Principal Metallurgist, Steel Image
June 2021
Even simple components, such as bolts, can fail for many reasons. For a root cause analysis (RCA), its critical that the failure mode be diagnosed. In fact, for any RCA, one of the first steps is diagnosing the failure mode based upon study of the failed component itself. Or else the RCA may not properly address the true root cause of failure. Although nothing will replace lab-based analysis by experts, several common failure modes to bolts can be recognized by visual examination alone with a bit of training.
The following is a summary of some of the more common causes of bolt failures, methods used to diagnose the failure mode.
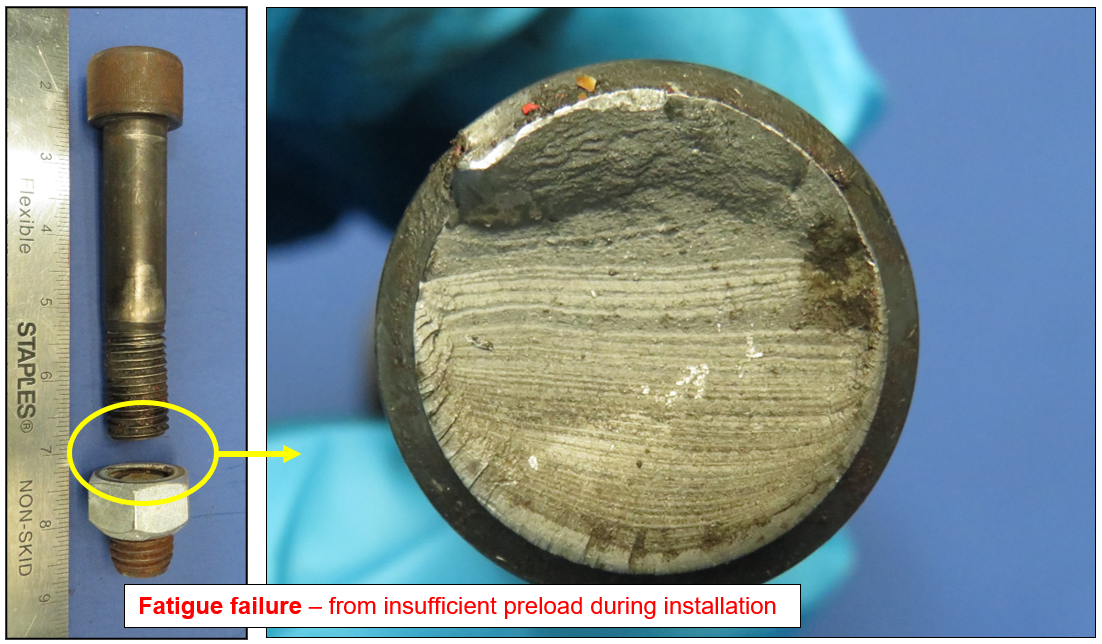
Fatigue Failure
The most common failure mode of bolts is fatigue failure. Bolts can fail by due to several reasons including (1) the bolt had not been sufficiently preloaded/tension during installation, (2) had lost its preload during service, (3) the applied cyclic loading had been excessive – far beyond the strength of the bolt and/or (4) the bolt had been understrength (quality issue/wrong grade).
Yet, before exploring these options, one must first confirm that the failure had been in fact by fatigue or they could be wasting their time in chasing the wrong issues. The primary method of diagnosing fatigue failure is examination of the fracture surface and recognizing its fatigue fracture features. Visual identification of fatigue can be learned with training.
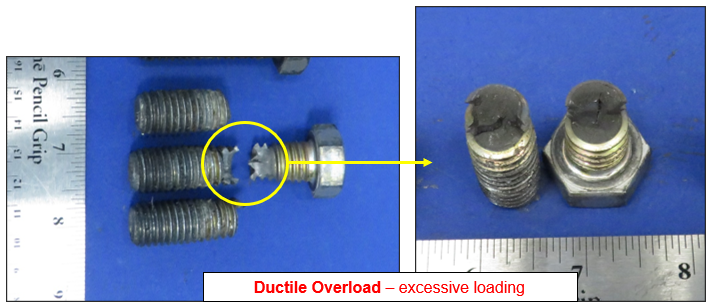
Ductile and Shear Overload
Ductile or shear failure can occur from either (a) over-torquing during installation, (b) an excessive loading event during service and/or (c) severely understrength bolts. Diagnosis of ductile and shear overload can also completed by visual examination once one knows what to look for. Once diagnosed as an overload failure, consider reviewing of the bolt/nut geometries, installation practices and the loading event at the time of failure. It is recommended to always test the bolt quality after shear failures (hardness, strength, confirm steel type, etc).
Once one learns how to recognize fatigue, ductile and shear overload, it accounts for the vast majority of bolt failures. There are numerous other damage mechanisms which we will discuss that can also cause bolts to fail, most of which require lab-based analysis to identify. Yet these are rare compared to mechanical failures. Which is why, if reliability professionals, maintenance or other engineers who deal with equipment failures were to learn to recognize/interpret mechanical failures, they would know in most cases what they are dealing with and if/what further lab investigation might be needed.
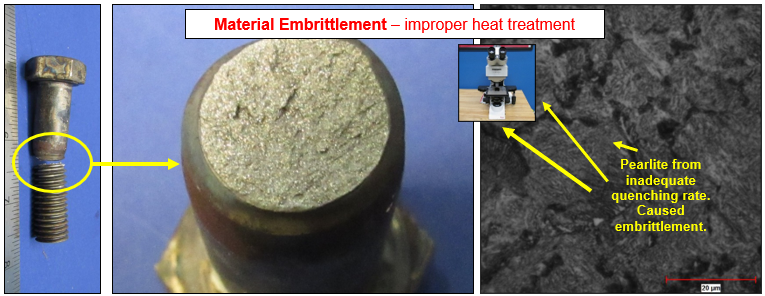
Material Embrittlement
Improper heat treatment and some service conditions can embrittle the steel, leaving the bolts susceptible to failure under low strain/bending loading or impact. Brittle fracture occurs during either installation, its first significant loading event or after years of degradation.
Brittle fracture forms visually recognizable fractures. However, visual examination alone does not provide the same degree of confidence as fatigue and ductile failures. Lab-based analysis is required to confirm brittle fracture and then assess why the material had failed in a brittle manner. Such as what embrittlement mechanism had permanently caused ductility loss. Once embrittlement is found and depending whether embrittlement was manufacture or service- based, one can assess whether all bolts in the same application are at risk. Or if an entire lot of bolts is at risk.
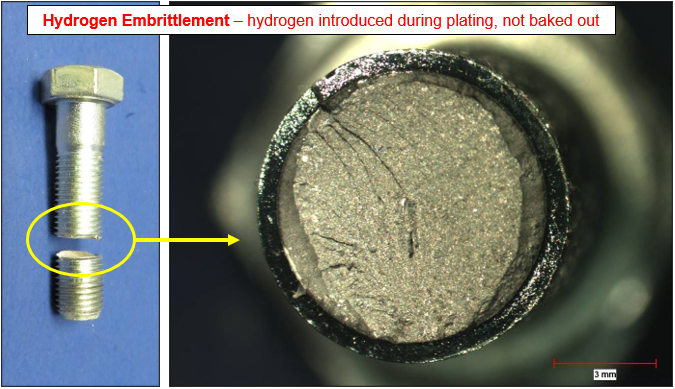
Hydrogen Damage
Some high strength bolts run the risk of hydrogen damage. Although called "hydrogen embrittlement", the term "embrittlement" is a bit misleading as crack growth over days or weeks while under tension rather than the material actually being brittle. Zinc or cadmium plated, high strength bolts with hardness values over 39 HRC are at the highest risk of hydrogen-based failures. The pickling and plating processes during manufacture can introduce hydrogen and the plating traps the hydrogen in. If not properly baked, entrapped hydrogen can result in delayed cracking days or weeks after installation. Hydrogen can also be introduced during service by some forms of corrosion.
Hydrogen embrittlement is diagnosed by examining the fracture surface, laboratory testing for hydrogen and evaluating the metallurgical condition of the bolt. Once diagnosed as hydrogen embrittle, the ongoing investigation would have to narrow down the source of hydrogen – either manufacture/plating or service-based corrosion.
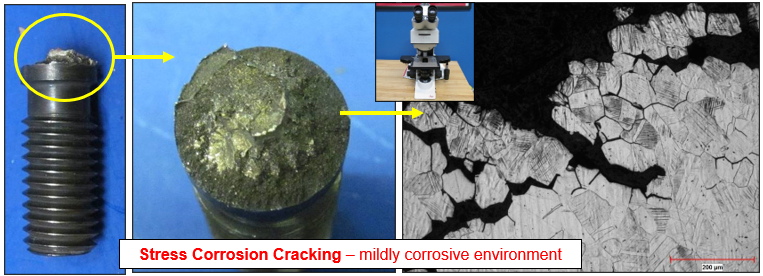
Stress Corrosion Cracking
Bolts being under constant tension leave them susceptible to stress corrosion cracking (SCC) if they are exposed to water-based corrosion agents. The effects of any corrosive environment are made worse at warmer temperatures. Over time, bolts exposed to the wrong compounds can begin to suffer cracking and eventually fail. Each material type is susceptible to different corrosion agents. Hardened carbon steels are at risk of SCC when exposed to a variety of compounds including ammonia, caustics and sulphur-based compounds. Stainless steels are most susceptible to chloride-based cracking.
The primary method used to diagnose stress corrosion cracking is by examination using an optical microscope. To determine the corrosion agents responsible for causing cracking, laboratory analysis often includes energy dispersive spectroscopy (EDS) analysis. If the bolts cannot be prevented from being exposed to similar corrosive conditions in the future, redesign or a change in bolt material type may be required to prevent future failures.
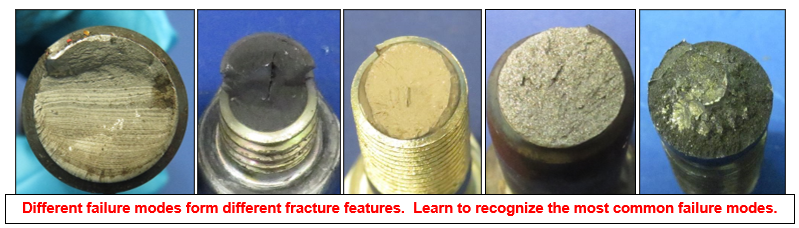
Summary and Takeaways
Fasteners can fail for a variety of reasons, each requiring notably different solutions to prevent repeat failures. One should never guess why a bolt failed because, if they did, they would sometimes guess wrong. Identifying the failure mode is critical to the success of a root cause analysis (RCA) in identifying why bolts failed and what efforts should be applied to prevent future failures.
Diagnosing the failure mode will always involve examining the failed bolt itself. There is no other way to be sure why it failed. Although nothing will replace the amount of information which can be learned by laboratories staffed by experts, with training a large amount of information can be learned by those closer to the field. In particular, fatigue and ductile overload can be learned to be recognized with relative confidence. Indications of brittle fracture can also be picked out visually too. In some cases, visual examination can be enough to diagnose how and why a bolt failed.
Although this article has summarized common failure modes for bolts, these concepts apply to all types of components and equipment. To understand how to prevent future failures of anything, one must understand how and why a part failed. For those involved with investigating or preventing equipment failures, learning to recognize the most common failure modes is critical to equipment reliability efforts.